“If it ain’t broke, don’t fix it.” You’ve probably heard this phrase a lot in your lifetime. That said, it’s not the best advice. You see, preventative maintenance is important. It’s better to “fix it” before a problem gets out of control and turns into a major issue!
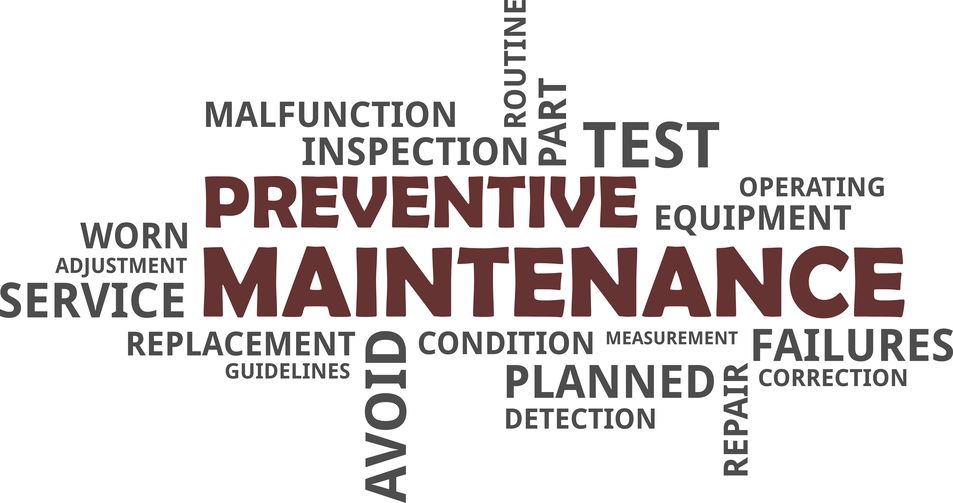
Many companies use CMMS software for their carefully designed maintenance program, and that’s a good thing. It’s smart to have maintenance performed at regular intervals, routinely, in order to avoid having to deal with larger, costly repairs “down the line.”
Why Preventative Maintenance is Important
Why is preventative maintenance important? Well, there’s the cost savings. You don’t want unplanned downtime where you have to halt a production line and miss deadlines, right? You also don’t want to damage your reputation. Therefore, preventative maintenance saves you money in the long run. Small fixes are less expensive than big fixes, and they don’t take up as much valuable time.
If you want improved safety (and who doesn’t?) then you want to work with good equipment that’s not going to injure workers. Therefore, preventative maintenance is good because it can improve the actual safety of the equipment which translates into fewer accidents and injuries on the job.
Increasing a piece of equipment’s efficiency is always a good thing, right? Preventative maintenance makes sure things like oil and fluid changes get done. Parts can be replaced before they totally wear out. Machines can be made to run at peak performance with greater reliability. Best of all, you’ll get less equipment downtime.
Finally, preventative maintenance helps with conservation of assets. This means your equipment will last longer for you.
When doing preventative maintenance tasks, laser alignment tools help identify misalignments and ultimately reduce machine wear, lost production time and breakdowns. Check out Seiffert Industrial’s laser alignment tools here; you can also call 800-856-0129 for more info.